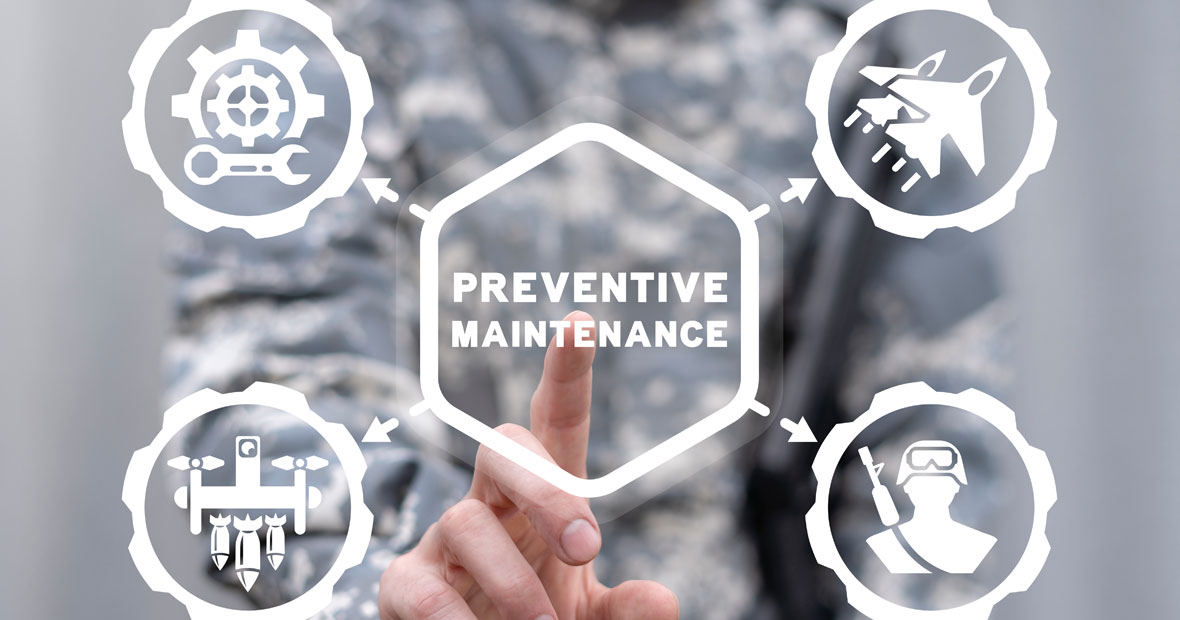
Semiconductor production is a crucial aspect of modern technology, as semiconductors are the building blocks of electronic devices. These devices include smartphones, computers, televisions, and many other everyday items that we rely on. Semiconductor production involves the fabrication of integrated circuits, which are comprised of numerous transistors and other electronic components embedded on a small piece of silicon. The process of manufacturing semiconductors is complex and requires precise control and sophisticated machinery.
Role of Preventive Maintenance in Semiconductor Manufacturing
Preventive maintenance plays a vital role in ensuring the smooth operation and efficiency of semiconductor production. This includes regularly inspecting, servicing, and maintaining equipment, even within specialized areas such as the semiconductor production machine reconditioning department, to prevent any potential issues before they escalate into major problems. Implementing a preventive maintenance program in semiconductor manufacturing offers several advantages.
Enhancing Equipment Efficiency
Preventive maintenance helps in enhancing equipment efficiency by ensuring that all machinery is functioning optimally. Regular inspections and servicing can identify and address any minor problems or wear and tear that may lead to decreased efficiency. By detecting and rectifying these issues early on, preventive maintenance ensures that equipment operates at its maximum potential, resulting in improved production output and quality.
Reducing Unplanned Downtime
Unplanned downtime can be extremely costly for semiconductor manufacturers. Equipment failures can result in production delays, disrupting the entire manufacturing process. Preventive maintenance helps in reducing unplanned downtime by identifying and fixing potential issues before they cause major equipment failures. By proactively maintaining equipment, semiconductor manufacturers can minimize the risk of unexpected breakdowns and ensure smooth production operations.
Mitigating Risk of Equipment Failure
Equipment failure in semiconductor production can have severe consequences, including loss of production and increased expenses for repair or replacement. Preventive maintenance plays a crucial role in mitigating the risk of equipment failure. By conducting regular inspections and servicing, any potential signs of equipment malfunction or deterioration can be detected early on. This allows for timely repairs or replacements before the situation worsens, resulting in reduced downtime and cost savings for manufacturers.
Challenges in Semiconductor Production Without Preventive Maintenance
Without the implementation of a preventive maintenance program, semiconductor production can face several challenges. These challenges include:
- Increased risk of equipment failure leading to production delays
- Higher maintenance costs due to reactive repairs
- Poor equipment efficiency and reduced production output
- Higher likelihood of safety hazards for personnel
- Difficulty in meeting quality standards and customer demands
These challenges can have a significant impact on the overall profitability and competitiveness of semiconductor manufacturers.
Benefits of Implementing Preventive Maintenance
Implementing a preventive maintenance program in semiconductor production offers several benefits that positively impact the manufacturing process. These benefits include:
- Increased equipment reliability and lifespan
- Improved equipment efficiency and production output
- Reduced unplanned downtime and production delays
- Lower maintenance costs with proactive repairs
- Enhanced safety for personnel working with machinery
- Consistent quality standards and customer satisfaction
By investing in preventive maintenance, semiconductor manufacturers can optimize their operations and achieve better overall performance.
Key Components of a Preventive Maintenance Plan in Semiconductor Production
An effective preventive maintenance plan in semiconductor production should encompass several key components:
Regular Equipment Inspections
Regular inspections are essential in detecting any signs of equipment deterioration or malfunction. These inspections should be conducted on a predetermined schedule to identify issues early on and prevent major breakdowns.
Accurate Record Keeping
Accurate record keeping is crucial in maintaining a comprehensive maintenance history for each piece of equipment. This includes recording details of inspections, servicing, repairs, and any other relevant information. These records help in tracking maintenance activities and identifying patterns or trends in equipment performance.
Scheduled Equipment Servicing
Scheduled servicing involves conducting routine maintenance activities, such as lubrication, cleaning, calibration, and component replacements. By following a predetermined schedule, semiconductor manufacturers can ensure that all necessary maintenance tasks are performed promptly.
Trained Personnel for Maintenance Tasks
Having trained personnel who are knowledgeable and experienced in maintenance tasks is critical for the success of a preventive maintenance program. These individuals should be well-versed in equipment troubleshooting, repair techniques, and safety protocols to effectively carry out maintenance activities.
By incorporating these key components into their preventive maintenance plan, semiconductor manufacturers can optimize equipment performance and minimize the risk of downtime and equipment failures.