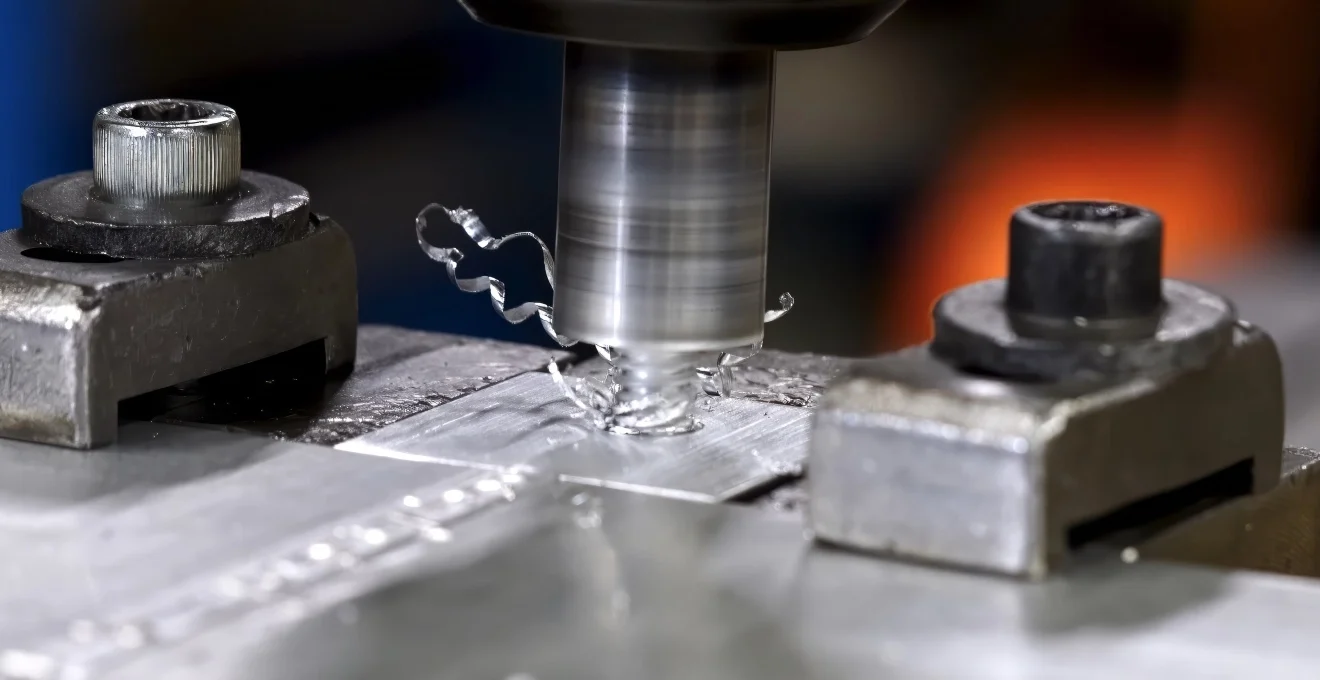
Friction stir welding (FSW) has revolutionized joining techniques in the aerospace industry, offering superior weld quality and mechanical properties compared to traditional fusion welding methods. As aerospace manufacturers strive for lighter, stronger structures, optimizing FSW tool design becomes crucial for enhancing process efficiency and joint integrity. This optimization process involves careful consideration of material selection, geometric features, and thermal management strategies to create tools capable of withstanding the extreme conditions encountered during welding of high-performance aerospace alloys.
Principles of tool design for friction stir welding in aerospace
The fundamental principles governing FSW tool design for aerospace applications center around maximizing material flow, minimizing tool wear, and ensuring consistent heat generation. Effective tool design is essential for producing high-quality, defect-free welds in aerospace-grade aluminum alloys, titanium alloys, and advanced composites. The friction stir welding tool must withstand extreme thermal and mechanical stresses while maintaining dimensional stability throughout the welding process.
Key considerations in FSW tool design include:
- Material selection for optimal wear resistance and thermal stability
- Geometric features that promote efficient material flow and heat generation
- Thermal management strategies to prevent tool degradation
- Adaptability to various joint configurations and material thicknesses
By addressing these factors, engineers can develop FSW tools tailored to the specific requirements of aerospace manufacturing, enabling the production of lightweight, high-strength structures essential for modern aircraft and spacecraft.
Material selection for FSW tools in aerospace applications
Choosing the right material for FSW tools is critical in aerospace applications due to the extreme conditions encountered during welding. The ideal tool material must possess excellent high-temperature strength, wear resistance, and thermal stability. Several advanced materials have emerged as frontrunners in FSW tool design for aerospace alloys:
Tungsten-based alloys for high-temperature resistance
Tungsten-based alloys, such as tungsten-rhenium (W-Re) and tungsten-lanthanum (W-La), offer exceptional high-temperature strength and thermal conductivity. These properties make them ideal for welding high-melting-point aerospace alloys like titanium and nickel-based superalloys. Tungsten-based tools can maintain their hardness and geometric stability at temperatures exceeding 1000°C, ensuring consistent weld quality throughout long production runs.
Polycrystalline cubic boron nitride (PCBN) for wear resistance
PCBN tools represent the pinnacle of wear resistance in FSW applications. With a hardness second only to diamond, PCBN can withstand the abrasive conditions encountered when welding reinforced aluminum composites and other challenging aerospace materials. While expensive, PCBN tools offer unparalleled longevity and consistency, making them cost-effective for high-volume production of critical aerospace components.
Nickel-based superalloys for corrosion resistance
Nickel-based superalloys like Inconel 718 and Hastelloy X provide an excellent balance of high-temperature strength, corrosion resistance, and toughness. These materials are particularly well-suited for FSW tools used in welding corrosion-resistant aerospace alloys or in environments where chemical reactivity between the tool and workpiece is a concern. The superior oxidation resistance of nickel-based superalloys also contributes to extended tool life in high-temperature applications.
Comparison of MP159 and inconel 718 for FSW tool performance
A comparative analysis of MP159 and Inconel 718 reveals the nuanced performance characteristics of these popular FSW tool materials:
Property | MP159 | Inconel 718 |
---|---|---|
Yield Strength (MPa) | 1720 | 1034 |
Maximum Service Temperature (°C) | 650 | 700 |
Thermal Conductivity (W/m·K) | 11.5 | 11.4 |
Corrosion Resistance | Good | Excellent |
While MP159 offers superior yield strength, Inconel 718 provides better corrosion resistance and can operate at slightly higher temperatures. The choice between these materials often depends on the specific aerospace alloy being welded and the production environment.
Geometric considerations in FSW tool design for aerospace alloys
The geometry of an FSW tool plays a crucial role in determining weld quality, material flow, and process efficiency. For aerospace applications, where precision and consistency are paramount, optimizing tool geometry can significantly impact joint performance and production costs.
Optimizing shoulder diameter for heat input control
The shoulder diameter of an FSW tool directly influences the amount of frictional heat generated during welding. Larger shoulder diameters increase heat input, which can be beneficial for welding thicker sections or high-melting-point alloys. However, excessive heat can lead to overaging in heat-treatable aluminum alloys commonly used in aerospace structures. Engineers must carefully balance shoulder diameter with rotational speed to achieve optimal heat input for each specific alloy and joint configuration.
Pin profiles: threaded vs. unthreaded for aluminum alloys
The choice between threaded and unthreaded pin profiles can significantly affect material flow and weld quality in aluminum aerospace alloys. Threaded pins promote vertical material movement, which is particularly beneficial for welding thicker sections. Unthreaded pins, on the other hand, may be preferable for thin sheets where excessive vertical flow could lead to thinning or defects in the weld nugget.
Scroll and spiral shoulder designs for improved material flow
Advanced shoulder designs incorporating scrolls or spirals can significantly enhance material flow and reduce defect formation in aerospace FSW applications. These features help to contain plasticized material within the weld zone, preventing flash formation and ensuring more consistent weld properties. Spiral shoulder designs have shown particular promise in welding dissimilar aluminum alloys, a common requirement in modern aircraft construction.
Tapered and stepped pin geometries for joint efficiency
Tapered and stepped pin geometries offer advantages in terms of material flow and joint efficiency, particularly for variable thickness joints often encountered in aerospace structures. Tapered pins provide a gradual transition in material flow, reducing the risk of defect formation at the weld root. Stepped pin designs can be tailored to accommodate specific joint configurations, ensuring adequate mixing throughout the weld thickness.
Thermal management strategies in FSW tool design
Effective thermal management is crucial for maintaining tool integrity and weld quality in aerospace FSW applications. As welding speeds and material thicknesses increase, so does the thermal load on the FSW tool. Implementing advanced cooling strategies and thermal barrier technologies can significantly extend tool life and improve process stability.
Implementing internal cooling channels in FSW tools
Internal cooling channels represent a significant advancement in FSW tool design for high-temperature aerospace applications. By circulating coolant through precisely designed channels within the tool body, engineers can maintain optimal tool temperature even under extreme welding conditions. This approach is particularly beneficial when welding titanium alloys or thick sections of aluminum, where heat buildup can lead to rapid tool wear or weld defects.
The design
of internal cooling channels requires careful consideration of fluid dynamics and heat transfer principles to ensure uniform cooling without compromising tool strength. Advanced computational fluid dynamics (CFD) simulations are often employed to optimize channel geometry and coolant flow rates.
Thermal barrier coatings for extended tool life
Thermal barrier coatings (TBCs) offer another avenue for enhancing FSW tool performance in aerospace applications. These specialized coatings, often composed of ceramic materials like yttria-stabilized zirconia (YSZ), create a protective layer that reduces heat transfer to the tool substrate. By lowering the thermal load on the tool, TBCs can significantly extend tool life and allow for higher welding speeds.
Modeling heat dissipation using COMSOL multiphysics
Accurate modeling of heat dissipation is essential for optimizing FSW tool design and process parameters. COMSOL Multiphysics software has emerged as a powerful tool for simulating the complex thermal interactions in FSW processes. By combining heat transfer, fluid dynamics, and structural mechanics modules, engineers can create comprehensive models that predict tool temperatures, material flow, and potential defect formation.
Advanced manufacturing techniques for FSW tool production
The evolution of manufacturing technologies has opened new possibilities for creating complex, high-performance FSW tools tailored to aerospace applications. Advanced production methods allow for the realization of intricate geometries and material combinations that were previously impractical or impossible to manufacture.
Additive manufacturing of complex FSW tool geometries
Additive manufacturing, particularly metal 3D printing technologies like selective laser melting (SLM) and electron beam melting (EBM), has revolutionized the production of FSW tools. These techniques enable the creation of tools with complex internal structures, such as conformal cooling channels, that optimize thermal management and material flow. The layer-by-layer construction process allows for the integration of features that would be challenging or impossible to produce using traditional machining methods.
Precision machining of PCBN tools using EDM technology
While PCBN offers unparalleled wear resistance for FSW tools, its extreme hardness presents challenges in manufacturing. Electrical discharge machining (EDM) has emerged as a preferred method for shaping PCBN tools with high precision. EDM allows for the creation of complex geometries and fine features without inducing the mechanical stresses associated with conventional machining techniques.
Surface treatment methods for enhanced tool performance
Surface treatments play a crucial role in optimizing FSW tool performance and longevity. Advanced coating and texturing techniques can enhance wear resistance, reduce adhesion of welded material, and improve thermal characteristics. Some of the most promising surface treatment methods for aerospace FSW tools include:
- Physical Vapor Deposition (PVD) of hard coatings like TiAlN or CrN
- Laser surface texturing to create micro-patterns for improved material flow
- Plasma nitriding for enhanced surface hardness and wear resistance
- Composite boride coatings for extreme temperature applications
These surface treatments can significantly extend tool life and improve weld quality, particularly in challenging aerospace alloys like titanium and nickel-based superalloys.
FSW tool design optimization for specific aerospace alloys
Tailoring FSW tool designs to specific aerospace alloys is essential for achieving optimal weld quality and process efficiency. Different alloy systems present unique challenges in terms of material flow, heat generation, and tool wear, necessitating customized approaches to tool geometry and material selection.
Tool designs for joining AA2024 and AA7075 in aircraft structures
AA2024 and AA7075 are widely used in aircraft structures due to their high strength-to-weight ratios. However, their different alloying elements and heat treatment responses require careful consideration in FSW tool design. Optimal tool designs for joining these alloys typically feature:
- Threaded, tapered pins to promote vertical material flow and minimize defect formation
- Concave shoulders with scrolls to contain plasticized material and reduce flash
- Tool materials with high wear resistance, such as MP159 or H13 tool steel with specialized coatings
Recent studies have shown that optimized tool designs can achieve joint efficiencies exceeding 90% of the base material strength in AA2024-AA7075 friction stir welds, a significant improvement over traditional fusion welding methods.
FSW tools for titanium alloys in aerospace components
Welding titanium alloys presents significant challenges due to their high strength, low thermal conductivity, and reactivity at elevated temperatures. FSW tool designs for titanium alloys must prioritize wear resistance and thermal management. Key features of titanium FSW tools include:
- Refractory metal alloys or PCBN materials for extreme wear resistance
- Simplified pin geometries to minimize tool stress and breakage
- Advanced cooling systems, such as internal liquid nitrogen channels
- Inert gas shielding to prevent oxidation of the tool and weld zone
Optimizing tool parameters for magnesium alloy AZ31 in aerospace applications
Magnesium alloys, particularly AZ31, are gaining interest in aerospace applications due to their ultra-low density. However, their low melting point and tendency to oxidize require specific considerations in FSW tool design. Optimal tool parameters for AZ31 typically include:
- Larger shoulder diameters to increase heat input and material plasticization
- Reduced rotational speeds to prevent excessive vertical flow that could lead to thinning or defects in the weld nugget.
- Reduced pin lengths to minimize heat generation and prevent melting
- Tool materials with lower thermal conductivity to control heat dissipation
Optimizing tool parameters for magnesium alloy AZ31 requires careful consideration of rotational speed, traverse speed, and plunge depth. Studies have shown that lower rotational speeds (600-800 rpm) and moderate traverse speeds (100-200 mm/min) tend to produce the best results in terms of weld quality and mechanical properties.
By tailoring FSW tool designs and process parameters to the specific characteristics of aerospace alloys, engineers can achieve significant improvements in weld quality, joint efficiency, and overall structural performance. This customized approach is essential for meeting the demanding requirements of modern aerospace manufacturing.
Advanced manufacturing techniques for FSW tool production
The evolution of manufacturing technologies has opened new possibilities for creating complex, high-performance FSW tools tailored to aerospace applications. Advanced production methods allow for the realization of intricate geometries and material combinations that were previously impractical or impossible to manufacture.
Additive manufacturing of complex FSW tool geometries
Additive manufacturing, particularly metal 3D printing technologies like selective laser melting (SLM) and electron beam melting (EBM), has revolutionized the production of FSW tools. These techniques enable the creation of tools with complex internal structures, such as conformal cooling channels, that optimize thermal management and material flow. The layer-by-layer construction process allows for the integration of features that would be challenging or impossible to produce using traditional machining methods.
Precision machining of PCBN tools using EDM technology
While PCBN offers unparalleled wear resistance for FSW tools, its extreme hardness presents challenges in manufacturing. Electrical discharge machining (EDM) has emerged as a preferred method for shaping PCBN tools with high precision. EDM allows for the creation of complex geometries and fine features without inducing the mechanical stresses associated with conventional machining techniques.
Surface treatment methods for enhanced tool performance
Surface treatments play a crucial role in optimizing FSW tool performance and longevity. Advanced coating and texturing techniques can enhance wear resistance, reduce adhesion of welded material, and improve thermal characteristics. Some of the most promising surface treatment methods for aerospace FSW tools include:
- Physical Vapor Deposition (PVD) of hard coatings like TiAlN or CrN
- Laser surface texturing to create micro-patterns for improved material flow
- Plasma nitriding for enhanced surface hardness and wear resistance
- Composite boride coatings for extreme temperature applications
These surface treatments can significantly extend tool life and improve weld quality, particularly in challenging aerospace alloys like titanium and nickel-based superalloys. For example, TiAlN coatings have been shown to reduce tool wear by up to 50% when welding high-strength aluminum alloys, leading to more consistent weld properties and reduced production costs.
FSW tool design optimization for specific aerospace alloys
Tailoring FSW tool designs to specific aerospace alloys is essential for achieving optimal weld quality and process efficiency. Different alloy systems present unique challenges in terms of material flow, heat generation, and tool wear, necessitating customized approaches to tool geometry and material selection.
Tool designs for joining AA2024 and AA7075 in aircraft structures
AA2024 and AA7075 are widely used in aircraft structures due to their high strength-to-weight ratios. However, their different alloying elements and heat treatment responses require careful consideration in FSW tool design. Optimal tool designs for joining these alloys typically feature:
- Threaded, tapered pins to promote vertical material flow and minimize defect formation
- Concave shoulders with scrolls to contain plasticized material and reduce flash
- Tool materials with high wear resistance, such as MP159 or H13 tool steel with specialized coatings
Recent studies have shown that optimized tool designs can achieve joint efficiencies exceeding 90% of the base material strength in AA2024-AA7075 friction stir welds, a significant improvement over traditional fusion welding methods. This high joint efficiency is crucial for maintaining the structural integrity of aircraft components under demanding flight conditions.
FSW tools for titanium alloys in aerospace components
Welding titanium alloys presents significant challenges due to their high strength, low thermal conductivity, and reactivity at elevated temperatures. FSW tool designs for titanium alloys must prioritize wear resistance and thermal management. Key features of titanium FSW tools include:
- Refractory metal alloys or PCBN materials for extreme wear resistance
- Simplified pin geometries to minimize tool stress and breakage
- Advanced cooling systems, such as internal liquid nitrogen channels
- Inert gas shielding to prevent oxidation of the tool and weld zone
Advances in FSW tool design have enabled successful welding of Ti-6Al-4V alloy with joint efficiencies approaching 95%, opening new possibilities for lightweight, high-strength aerospace structures.
These high-efficiency joints in titanium alloys are particularly valuable for aerospace applications where weight reduction and structural integrity are paramount, such as in next-generation aircraft frames and spacecraft components.
Optimizing tool parameters for magnesium alloy AZ31 in aerospace applications
Magnesium alloys, particularly AZ31, are gaining interest in aerospace applications due to their ultra-low density. However, their low melting point and tendency to oxidize require specific considerations in FSW tool design. Optimal tool parameters for AZ31 typically include:
- Larger shoulder diameters to increase heat input and material plasticization
- Reduced rotational speeds to prevent excessive heat generation and material softening
- Shorter pin lengths to minimize the heat-affected zone and maintain material properties
- Tool materials with excellent wear resistance and low reactivity with magnesium
Research has shown that FSW tools designed specifically for AZ31 can produce welds with tensile strengths up to 97% of the base material, making them suitable for critical aerospace components where weight reduction is a primary concern. The ability to effectively join magnesium alloys opens new avenues for ultra-lightweight structural designs in aircraft and spacecraft, potentially leading to significant improvements in fuel efficiency and payload capacity.
By tailoring FSW tool designs and process parameters to the specific characteristics of aerospace alloys, engineers can achieve significant improvements in weld quality, joint efficiency, and overall structural performance. This customized approach is essential for meeting the demanding requirements of modern aerospace manufacturing and pushing the boundaries of what is possible in aircraft and spacecraft design.